While the demand for electronic chips has been massively outscaling their supply for some time now, further problems in the supply chain are starting to arise as car manufacturers race to offer customers fully electric variants of their vehicles. The main issue now is the lack of specific metals, necessary for the production of electric car batteries and other components vital for powering a vehicle with electricity. This is significantly slowing down the research and development of new electric vehicles. However, with the EU preliminary deadline for all vehicles being electric set to 2035, it seems likely that brands will do anything to get their hands on the materials necessary for adapting to the coming shift in the market. Thus, the price of these metals, as well as any current electric vehicles, will presumably skyrocket in the coming years, until a new reliable supply chain is formed. An alternative to buying overpriced metals needed for production could be an improvement in recycling. Today most old parts of electric vehicles end their journey at a junkyard. With current technology, they are hard to recycle. Thus manufacturers have no choice but to buy freshly mined metals. These metals are in such a high demand, that they are often mined unethically towards the workers and the environment. In the Democratic Republic of Congo, one of the biggest suppliers of copper, graphite and nickel, child workers often work in terrible conditions, and ancient forests full of wildlife are sacrificed for precious metals, according to the Coface insurance company.
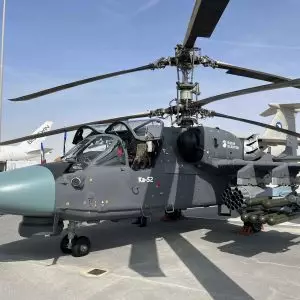